HIGH PERFORMANCE MOTION CONTROL
AND DATA ACQUISITION SOLUTIONS
We provide advanced software and electronics that convert your Machine Tool ideas into reality
MEET THE TEAM
HOW CAN WE HELP YOU?
We’d love to learn about your project and discuss how Polaris Motion can help.
Recent Articles
How can we help you?
We’d love to learn about your project and discuss how Polaris Motion can help.
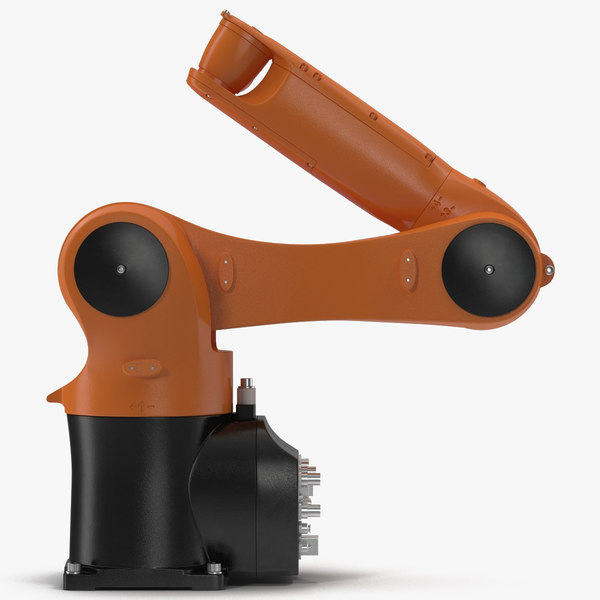
Technical Support
Our number one priority is to support our customers using the latest tools. We answer all questions in a timely manner to enable our customers to deliver their machines into their markets as fast as possible.
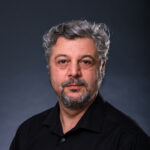
Business Development
For people new to our website, we welcome you. Feel free to browse around and If you have any questions about our company or our products, we are happy to answer them.